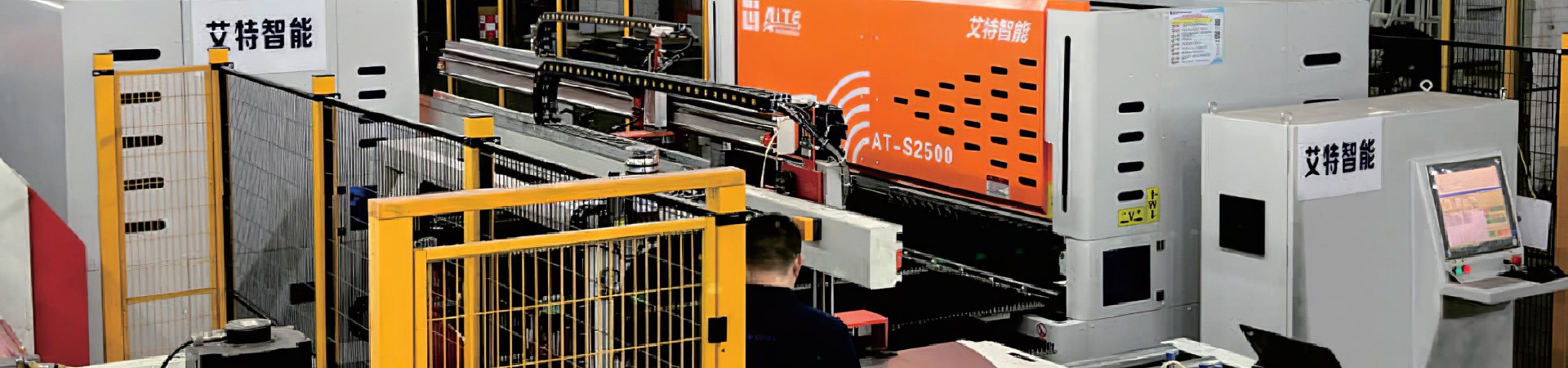
-
Home>
-
PRODUCTS>
-
Panel Bender>
The automatic sheet bending machine employs a servo clamping method, ensuring stable feeding and enhancing product processing accuracy. Unlike manual bending where errors may occur, the mechanical arm of the automatic sheet bending machine ensures error-free bending, guaranteeing the quality of batch-processed products.
The fully automatic panel bending center, independently developed by Aiotek, revolutionizes traditional bending methods, offering unparalleled precision, efficiency, cost-effectiveness, and safety.
1. High Accuracy:
The automatic sheet bending machine employs a servo clamping method, ensuring stable feeding and enhancing product processing accuracy. Unlike manual bending where errors may occur, the mechanical arm of the automatic sheet bending machine ensures error-free bending, guaranteeing the quality of batch-processed products.
2. High Efficiency:
Manual bending processes often suffer from inefficiencies due to the need for workers to manually lift large plates, leading to synchronization errors. However, the automatic bending center eliminates the need for manual lifting, thus preventing asynchronous operations and improving production efficiency. Moreover, equipped with universal molds, it eliminates the frequent need for upper and lower mold replacements, saving manpower and enhancing efficiency. Additionally, with fully automatic positioning, the center achieves a rapid bending efficiency of 0.2s/cut, ensuring continuous high-speed production.
3. High Security and Ease of Operation:
Compared to traditional methods, the fully automatic bending center eliminates the need for manual lifting throughout the process, minimizing the risk of staff injuries due to improper handling and ensuring overall safety during bending operations. Furthermore, equipped with intelligent programs, the center facilitates user-friendly operation even for staff without professional skills.
The automatic panel bending machine enhances bending efficiency and quality, streamlining operations, saving manpower and materials, maximizing processing speed, and ultimately boosting efficiency, cutting costs, and enhancing quality for enterprises.
Technical Parameters | AT-S3000 | Technical Parameters | AT-S3000 |
Feeding Structure | C-Type Upper Arm | Total Power | 84KW |
Bending Length | 3000mm | Average Power | 4KW |
Maximum Bending Height | 170mm | Workbench Structure | Brush & Rolling Bead |
Minimum Bending Height | 4mm | Speed Adjustment | Standard |
Min. Inner Size of Four-side Bending | 160mm*280mm | Advanced Command | Standard |
Min. Inner size of One-side Bending | 160mm | Arc Command | Standard |
Minimum Arc Radius | 2mm | Loading Robot Interface | Standard |
Minimum Continuous Bending Speed | 0.2s | Vacuum Pump | Optional |
Bending Angle | -90°~ 90° (> 0.8mm) 0°~ 180° (≤0.8mm) | Hinge Tooling | Optional |
Axes Controllable | Customized (18) | Equipment Size | 6700mm*3800mm*2320mm |
Maximum Feeding Speed | 120m/min | Equipment Weight | 20Ton |
Material | Max. Thickness(mm) |
Stainless Steel(SS) | 1.0 |
Carbon Steel (MS) | 1.2 |
Aluminum(AL) | 2.5 |